He is kind of the grandfather of Agile and thus a relevant influence for modern software development methods: W. Edwards Deming
I have heard of Deming every once in a while. It is inevitable when you try to understand Agile and its Lean roots. Yet, whenever I read about him, I had the feeling I was misunderstanding him. His use of words felt slightly off. Maybe he uses different meanings and assumptions than I do? His prominence suggests that it would be worthwhile to dig deeper, so I bought his book "The New Economics".
Deming himself considers the heart of this book a transformation of companies in four aspects:
- Appreciation for a system: Management needs to understand that a company is a system. You cannot achieve the optimal setup for a system by optimizing the parts independently.
- Knowledge about variation: Management needs to understand that variation is normal. You must handle normal variation differently than special cases.
- Theory of knowledge: Apply scientific thinking to management. Before changing something you must have a theory that predicts what will happen. If the outcome is different than the theory, you learn something.
- Psychology: Humans are parts of the system, so you need to understand how humans react. Psychology provides counter-intuitive insights. For example, if you reward good performance then performance can get worse. Psychological safety is necessary for great teams.
This is high-level advice to which nobody would disagree today. On the other hand its is still easy to find examples today where these things went wrong. They are simple but not easy.
Quality
At the start of the book Deming laments about the quality of US products. His definition of quality:
A product or a service possesses quality if it helps somebody and enjoys a good and sustainable market.
This is not how I would define it. I usually prefer a definition which suggests measurability, like "degree to which the product/service fulfills the requirements". You can even find a formula like SQ=P-E, which says service quality is the difference between expectations and performance.
Wikipedia describes Demings definition of quality as "results of work efforts divided by total costs" and summarizes his philosophy as:
When people and organizations focus primarily on quality, defined by the following ratio, quality = Results of work efforts per total costs, quality tends to increase and costs fall over time. However, when people and organizations focus primarily on costs, costs tend to rise and quality declines over time.
My understanding is that Demings "quality" is "value added". A company transforms incoming supplies into output. Hopefully, the output has more value than the inputs and the effort to transform them, otherwise the company will be bankrupt soon. This fits the first definition directly from his book. In contrast, any good engineer will always have ideas how to improve the quality of a product, but if the customers do not value that then it does not improve quality in Demings sense of the word.
You cannot divide and delegate this quality to lower levels, since it is the aim of a system and you cannot optimize a system by optimizing parts individually.
System Thinking
Demings definition of a system:
A system is a network of interdependent components that work together to try to accompĺish the aim of the system.
This implies that there must be at least two components and there must be an aim.
Deming believes that a system require cooperation. If the components compete with each other it will destroy the system because it does not work at its full potential. He considers it necessary to manage a system otherwise (due to western culture) components will compete.
Maybe a system diagram is more important than an org chart? An org chart tells you, who you report to. A system diagram tells you, who you work with.
Deming shows a system of quality improvement in Fig. 6 which ignited Japans industrial revolution in 1950.
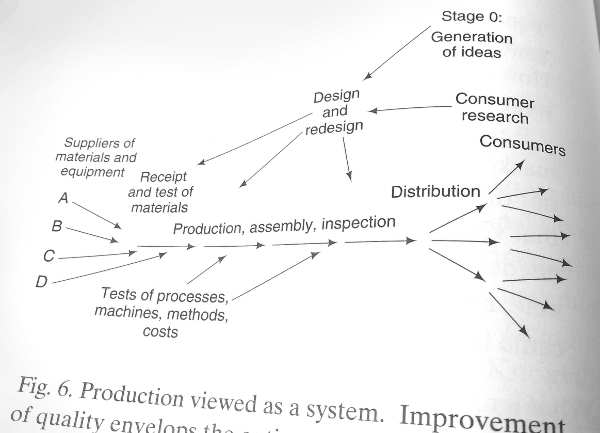
Fig. 7 is like Fig. 6 but the descriptions are put in boxes. The caption says "The system is destroyed". Just by drawing separating lines, you introduce competition which is harmful for the system over time. This is an observation with much evidence: If you separate humans into groups, an ugly "us vs them" mentality starts. Lesson: If you draw the system you are working in do not draw teams or departements. Instead draw the activities. Will try that at work.
Deming is a fan of monopolies because there is no competition and thus high efficiency. Good examples are: Bell Telephony Labs. Competitive companies have redundancies and thus form a less efficient system. However, it assumes that the monopoly still has the right aim though, but a monopolist often changes its aims. The incentives that make the customers happy get lost. I do not know how Deming would argue that.
Rating
The book is a introduction to Demings work and suitable for a broad audience. This means it does not contain technical details, e.g. on the statistical tools he used. As a computer scientist I'm used to much denser texts and the book does feel repetitive and too simplified sometimes. I did not learn anything directly applicable. The book did give me a better feeling about these process improvement topics and for that it was worth it. For example, it helps to understand where CMMI, ASPICE, and other standards come from. They are later iterations of the general ideas Deming pursued.